Revolutionary AI For Manufacturing Efficiency — No Big Data Needed
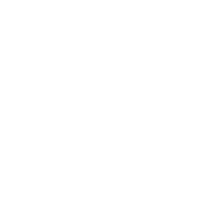
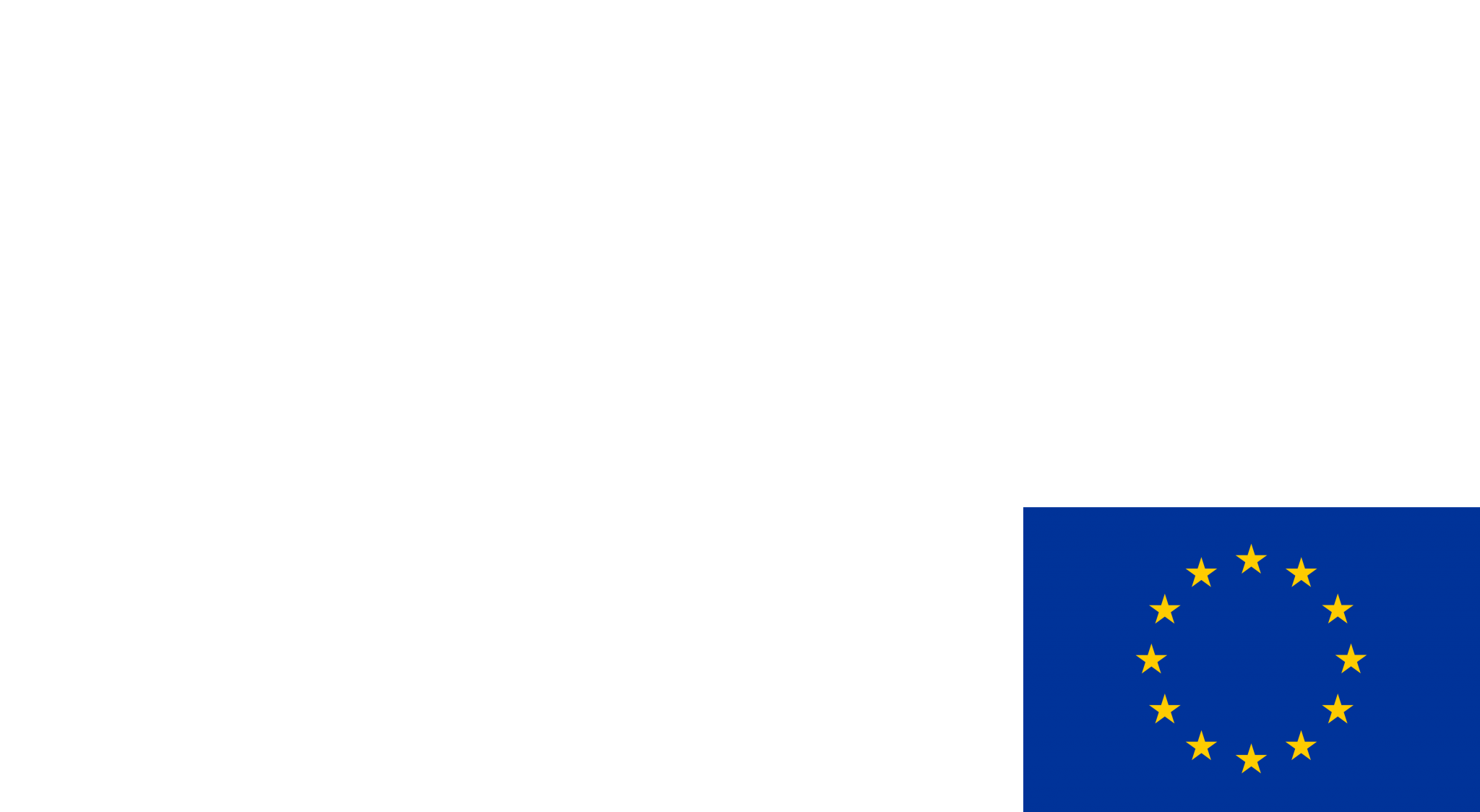
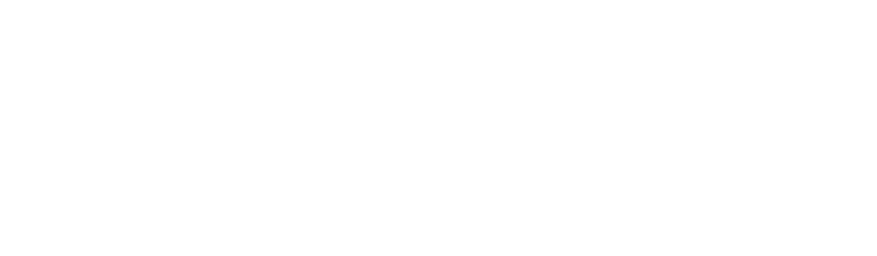
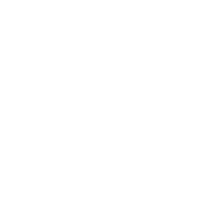
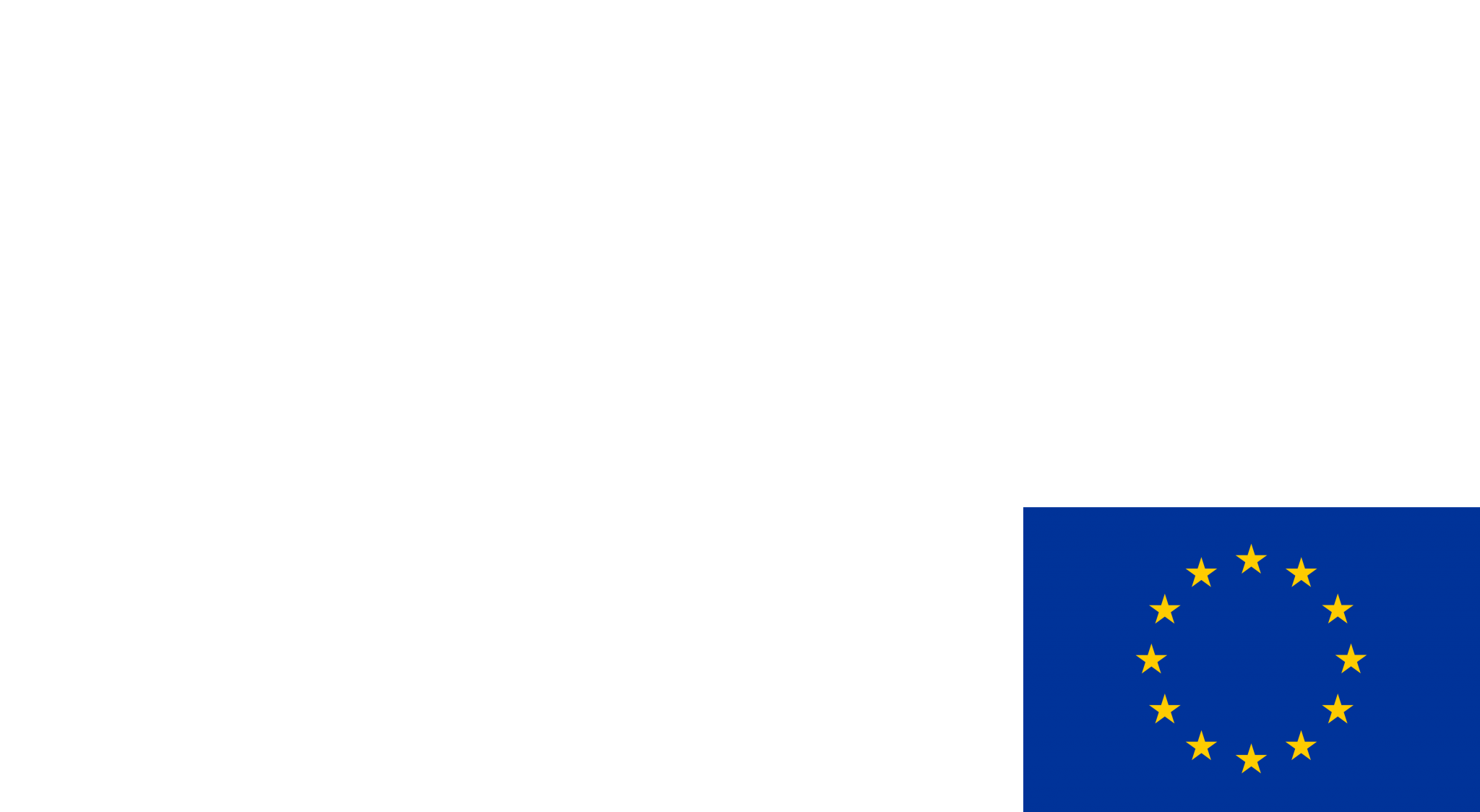
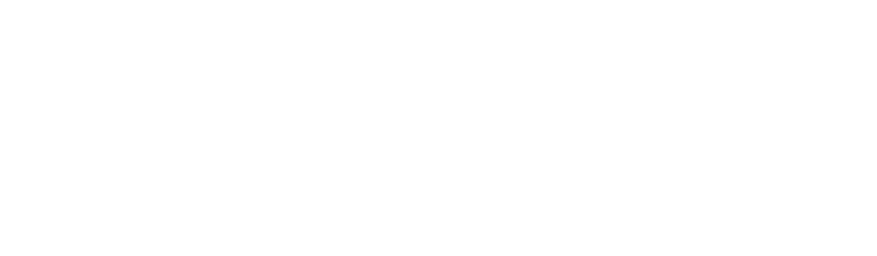
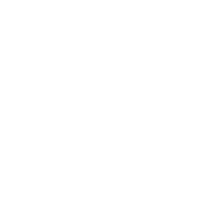
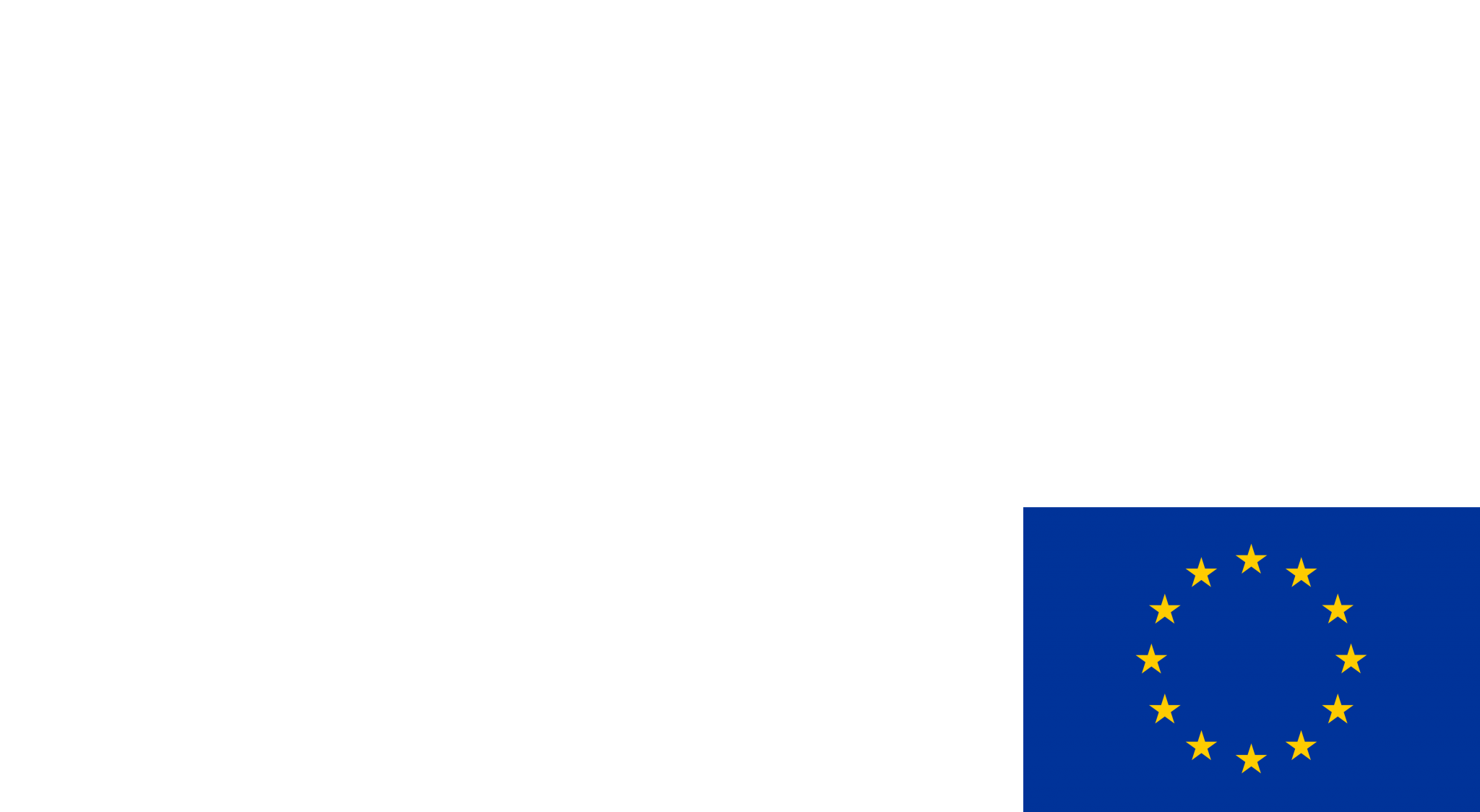
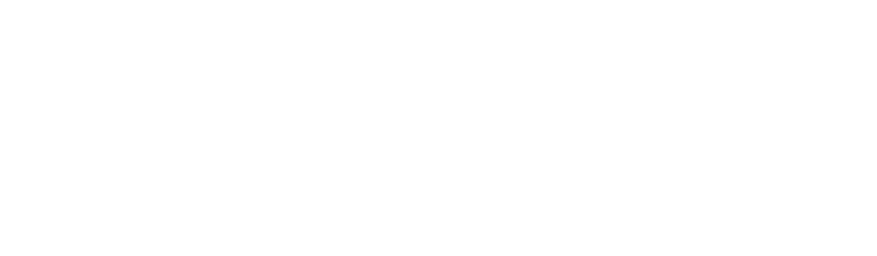
Paradigm Shift In Building Intelligent Industrial AI
Our Reinforcement Learning-based AI model training accelerates adoption, saving clients thousands of hours in data collection and millions in initial costs.
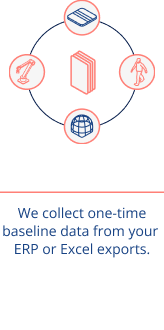

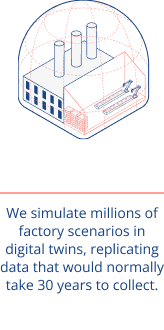

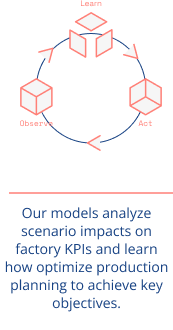

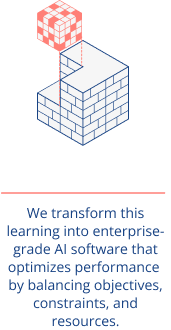

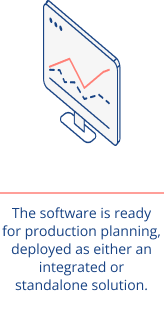
Seamless Integration Within 6 Weeks
Our AI is designed to integrate seamlessly with the systems you are already using.
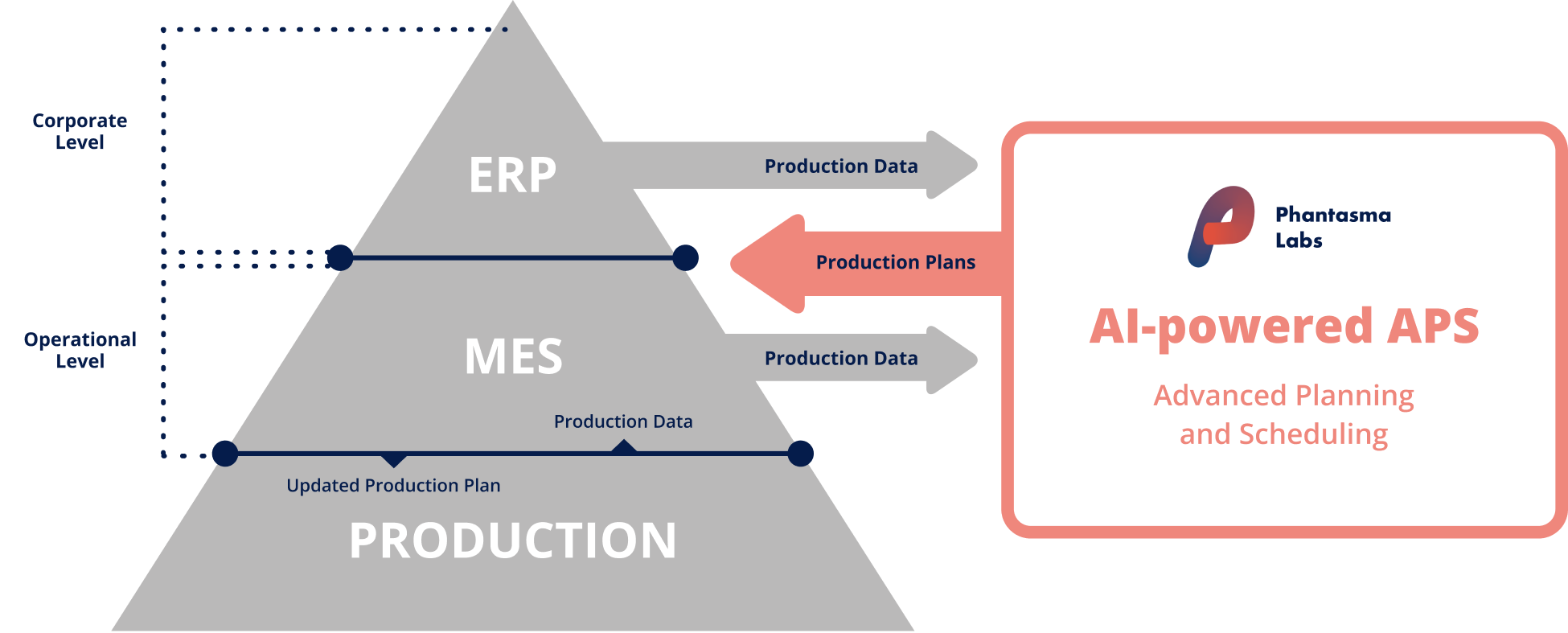
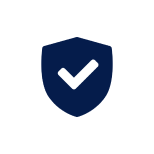
Our enterprise-grade technology is GDPR-compliant and meets strict cybersecurity and data protection standards.
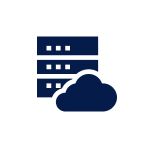
Our solution can be deployed on-premise or securely on any cloud.
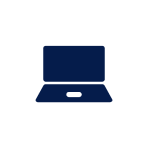
Our software requires minimal computing power and runs seamlessly on a standard laptop.
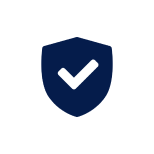
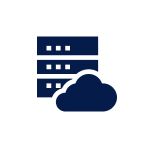
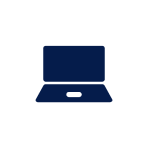
We Need Minimal Data To Get Started
The data we need is already available within your ERP system or stored in Excel sheets.
We Set a New Benchmark
In Production Planning Performance
Our solution beats industry benchmarks and clearly outperforms traditional methods and operations research tools.

Our Features Are
Designed To Meet Your Practical Needs
Implemented In 6 Weeks,
ROI Delivered In Just 6 Months
Our innovative approach to AI model training ensures quick AI adoption in factories. We deliver and integrate tailored production planning features into your systems in 4 to 6 weeks, with customers typically seeing ROI within 6 months.
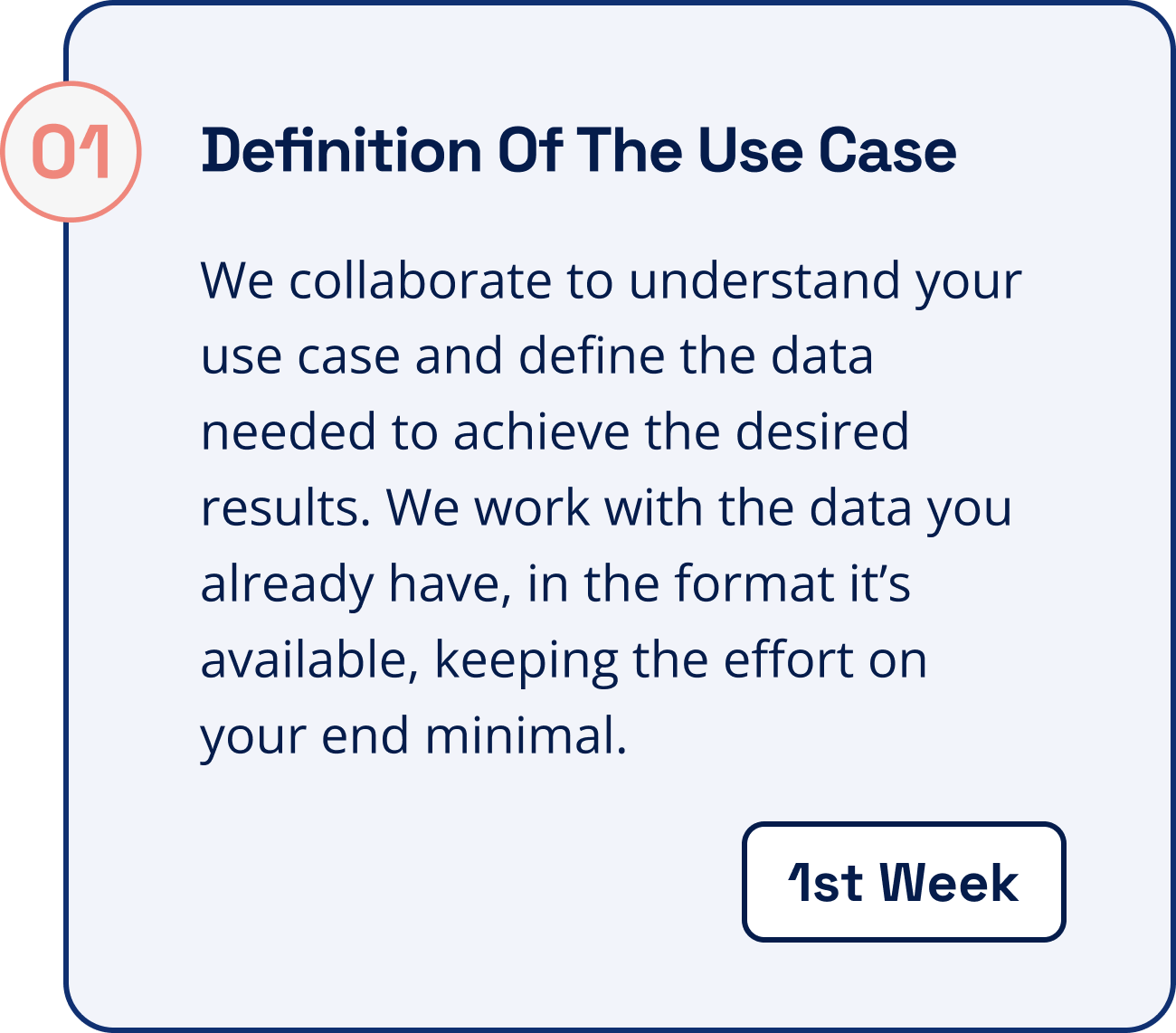
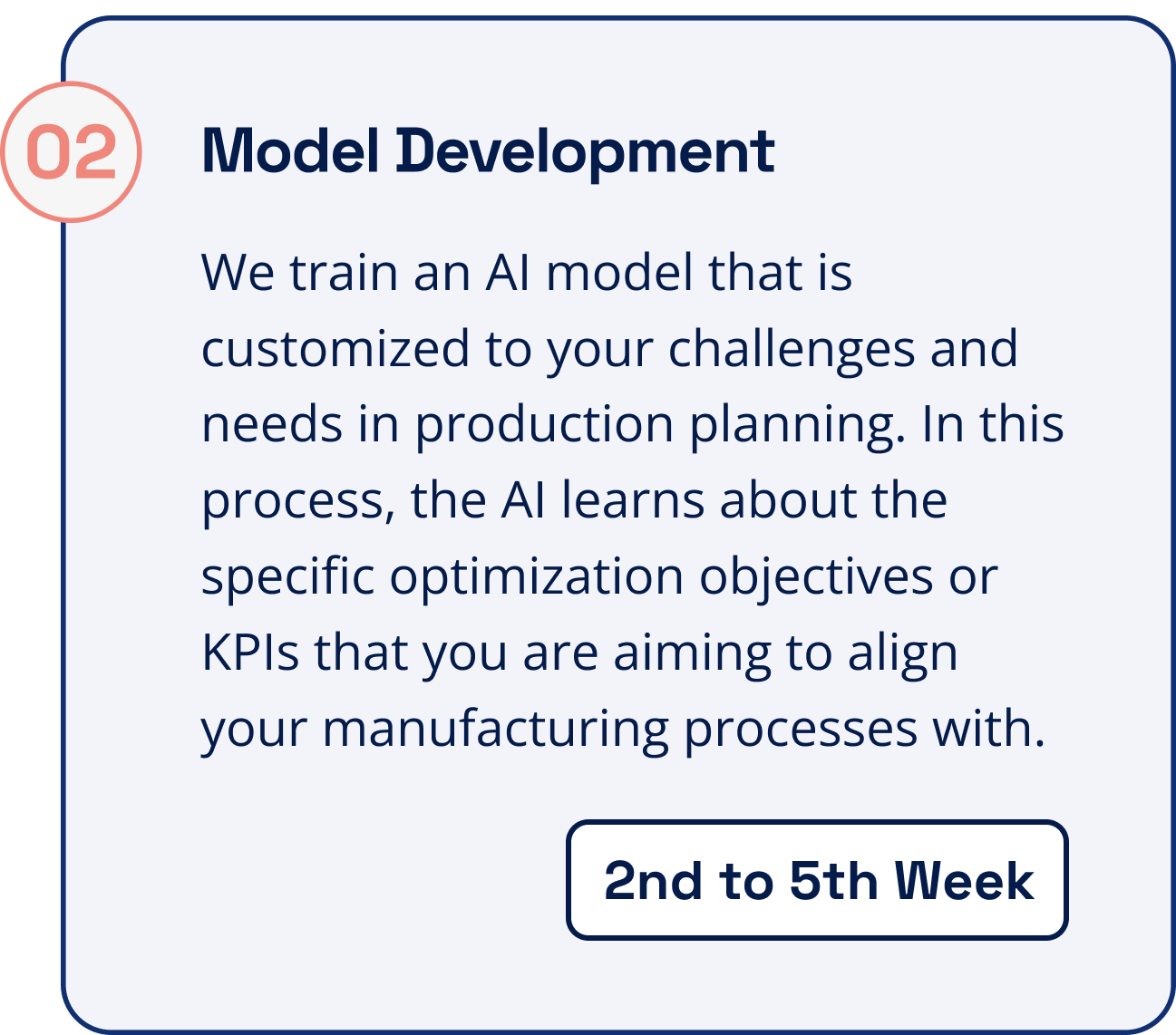
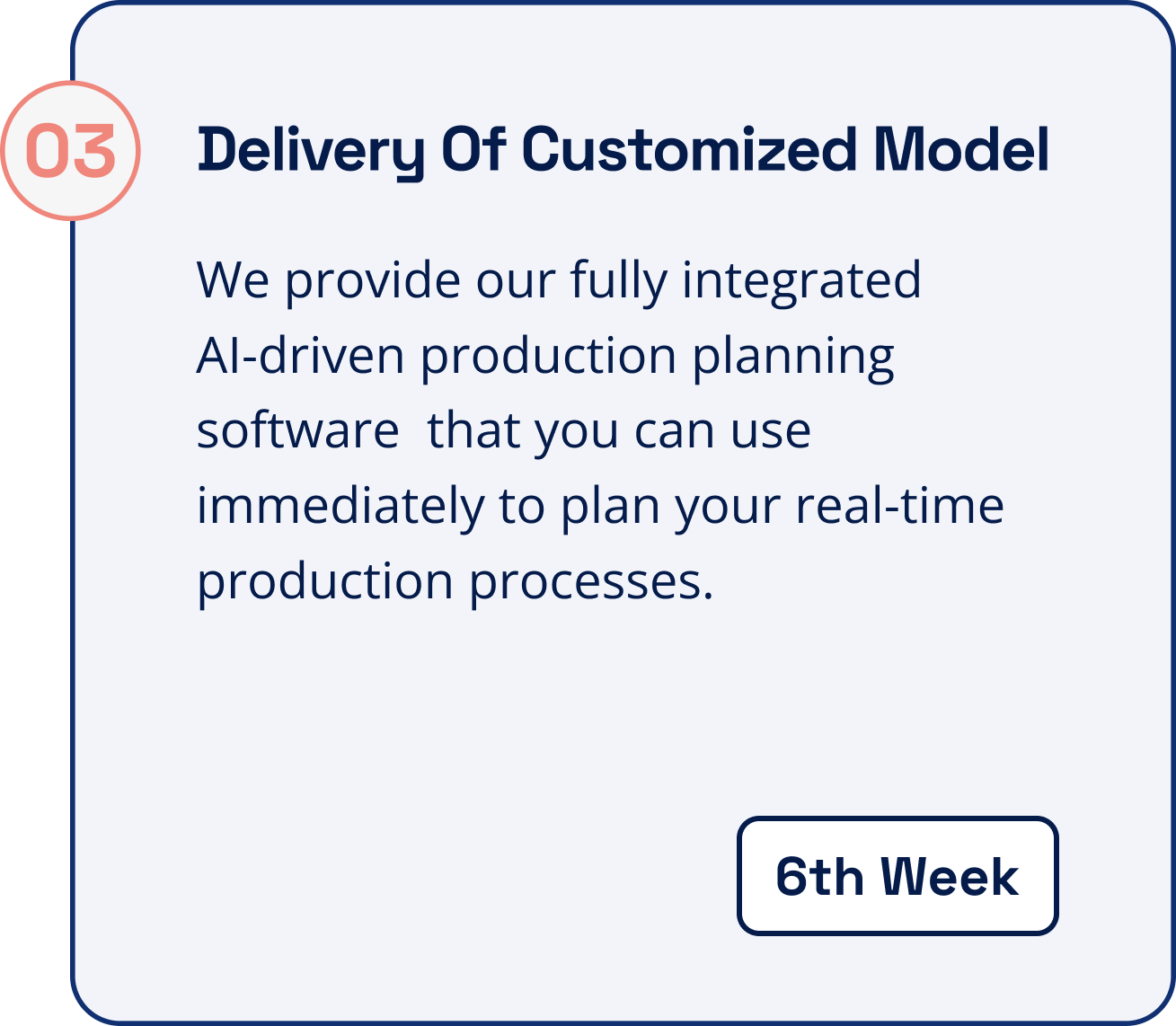
Keep Using Your Favorite Tools
Contact us to learn how we can integrate with any ERP or MES.
See how AI scheduling was integrated into Vectotax' ERP planning board ➔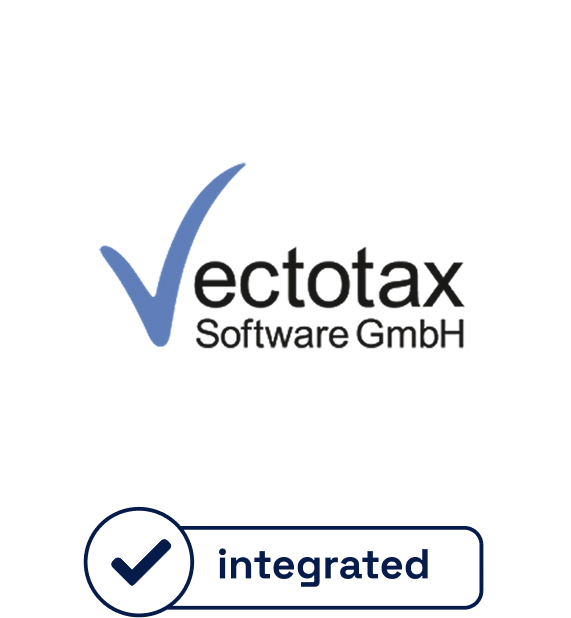
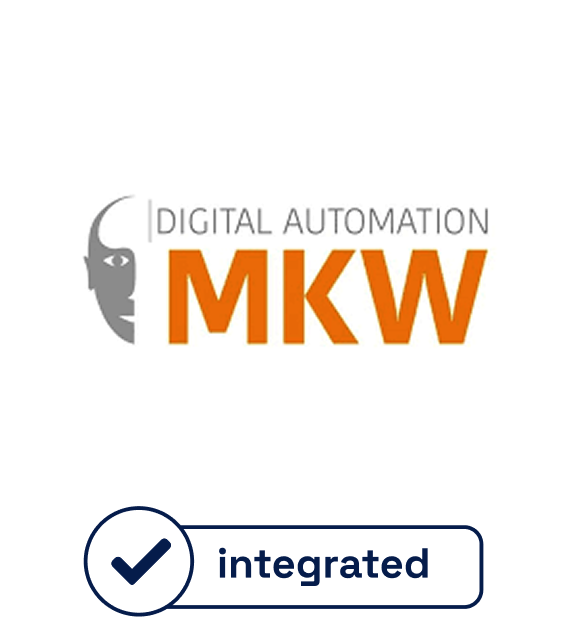
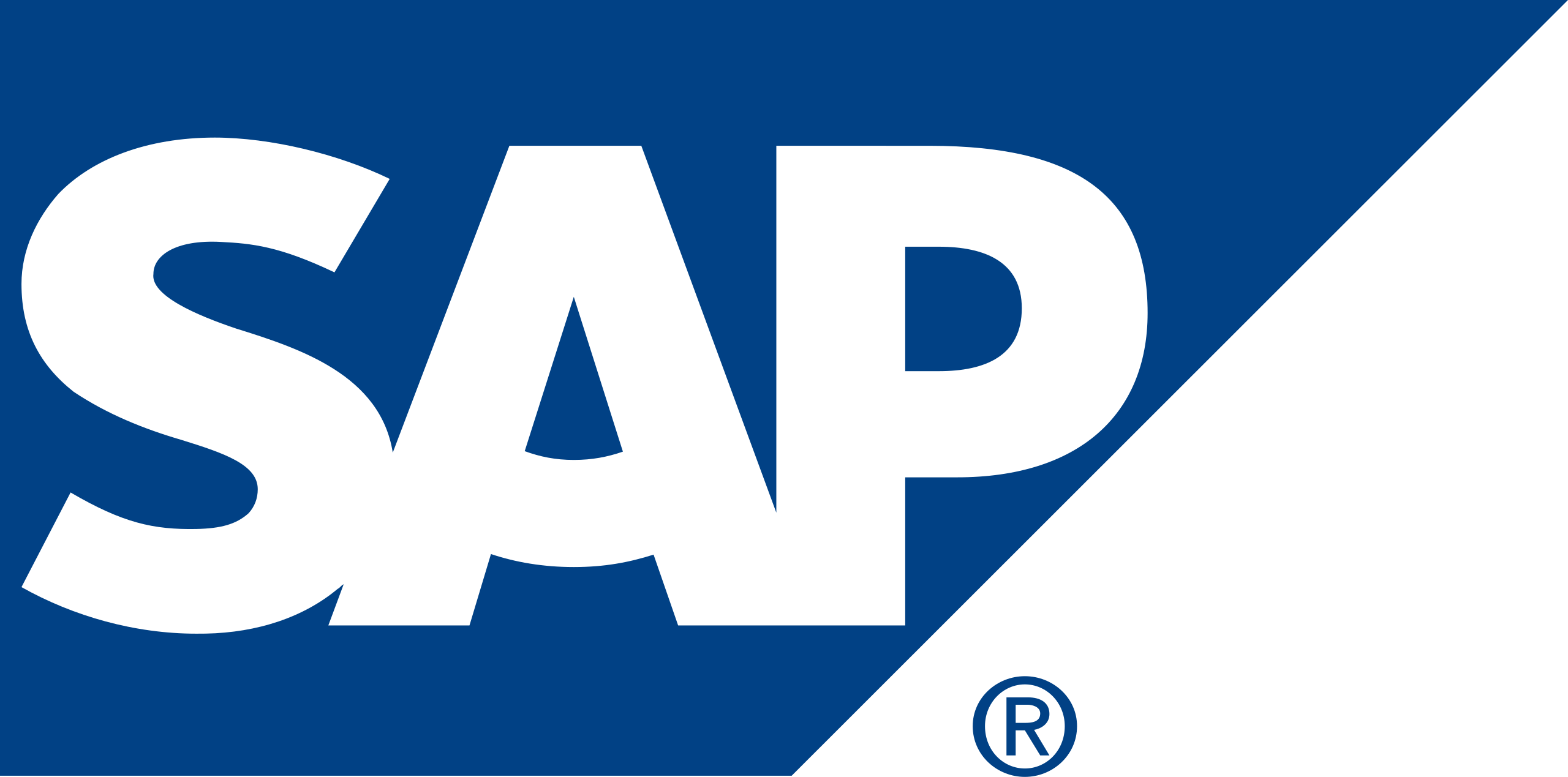
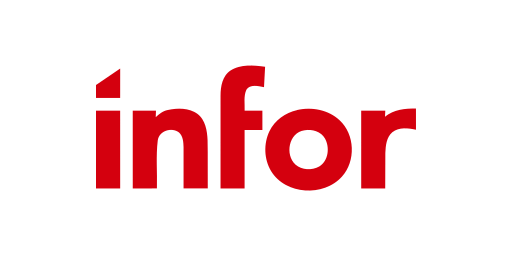
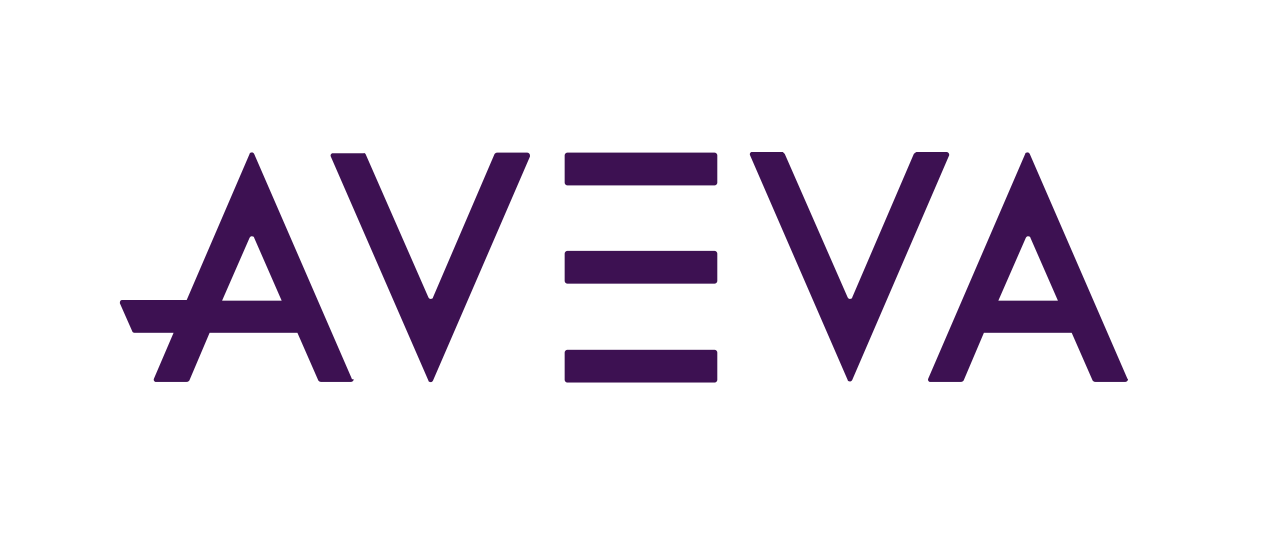
.png)
AI Solutions By Phantasma
Latest News
Explore the latest news from Phantasma as well as our articles on Industrial AI, Smart Planning and Production Optimization.